How Steel is Made
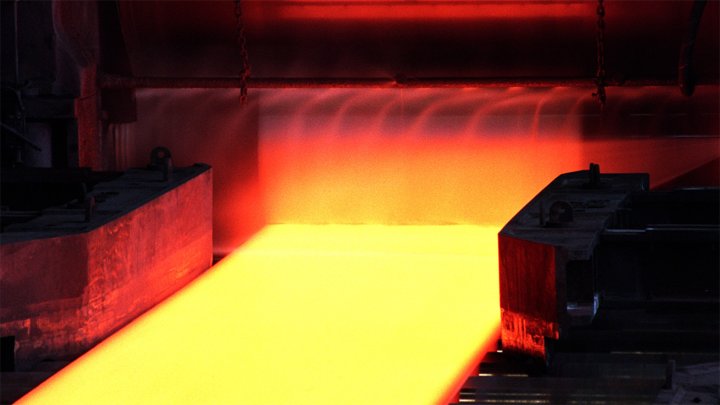
Global steelmaking – key production routes1
Steel is produced via two main routes: the blast furnace-basic oxygen furnace (BF-BOF) route and electric arc furnace (EAF) route. Variations and combinations of these production routes also exist.
The key difference between the routes is the type of raw materials they consume. For the BF-BOF route these are predominantly iron ore, coal, and scrap steel, while the EAF route produces steel using mainly scrap steel and electricity. Depending on the plant configuration and availability of recycled steel, other sources of metallic iron such as direct-reduced iron (DRI) or hot metal can also be used in the EAF route.
Blast furnace-basic oxygen furnace - BF-BOF (primary steelmaking)
A total of around 71% of global steel production is produced using the BF-BOF route2. First, iron ores are reduced to iron, also called hot metal or pig iron. Then the iron is converted to steel in the BOF, this stage may include the addition of scrap steel. Scrap has a cooling effect on the steelmaking process so there is a thermodynamic limit to how much can be used (up to ~30%3). After casting and rolling, the steel is delivered as coil, plate, sections or bars.
At Port Kembla Steelworks, NSW, BlueScope currently uses the BF-BOF steelmaking method to manufacture flat steel products. See ‘Future of Steelmaking’ below for information on BlueScope’s future plans.
Electric arc furnace - EAF (secondary steelmaking)
Steel made in an EAF uses electricity to melt scrap steel. This is commonly supplemented by other sources of metallic iron such as direct-reduced iron (DRI). Additives, such as alloys, are used to adjust to the desired chemical composition. Electrical energy can be supplemented with oxygen injected into the EAF. Downstream process stages, such as casting, reheating and rolling, are similar to those found in the BF-BOF route. About 29% of global steel is produced via the EAF route4.
Complementary production routes
Most steel products remain in use for decades before they can be recycled. Therefore, there is not enough recycled steel to meet growing demand using the EAF steelmaking method alone. Demand is met through the combined use of the BF-BOF and EAF production methods. BlueScope has three steelmaking sites globally: Port Kembla Steelworks in NSW, Australia, Glenbrook in Auckland, New Zealand and North Star in Delta, Ohio in the USA. In each of these geographies, we utilise different production routes.
Future of steelmaking
Climate action is key to BlueScope’s Purpose and is a core element of our Corporate Strategy: building a pathway to low emission-intensity iron and steelmaking in Australia is a key priority for our business.We believe Direct Reduced Iron (DRI) is the most prospective technology to decarbonise our Australian business. We are investigating accelerated technology developments in natural gas Direct Reduced Iron (DRI) as a transitional pathway to using green hydrogen to produce lower emissions steel. For information on the future of steelmaking and climate action at BlueScope, including decarbonisation activity at Port Kembla Steelworks, see our Climate Action page.
Notes:
- Information sourced from What is steel? - worldsteel.org
- Source: 2023 World Steel in Figures using 2022 data
- Source: #steelFacts - worldsteel.org
- Source: 2023 World Steel in Figures using 2022 data
Further Information
See the following articles: