Decarbonisation update - Project NeoSmelt
At BlueScope, we’re committed to actively addressing climate change and investing in greenhouse gas emissions reduction to transform our organisation for long-term success. In the near to mid-term, we’re optimising current operating assets across our portfolio. For the longer term, we’re exploring and collaborating to pursue emerging technologies as we work towards our 2050 net zero goal.1
Decarbonisation in the iron and steel industry will require a range of perspectives, expertise, and partnerships across our value chain. We have formed numerous partnerships with industry leaders to support this process.
Project NeoSmelt pilot location announced
BlueScope, alongside Australia’s two largest iron ore miners, BHP and Rio Tinto, has selected the Kwinana Industrial Area, south of Perth, as the location to develop Australia’s largest ironmaking electric smelting furnace2 (ESF) pilot plant. This groundbreaking project, which aims to test the technology for producing iron without the need for traditional blast furnaces, sees BlueScope, BHP, Rio Tinto and Woodside Energy come together to try to accelerate the decarbonisation of steelmaking.
The collaboration project, called NeoSmelt, is investigating the development of a pilot-scale R&D facility to demonstrate that direct reduced iron (DRI) produced from Pilbara iron ore can be processed into iron suitable for steelmaking in an ESF. If proven, the DRI-ESF process could provide a feasible pathway towards low emissions iron and steelmaking for the global steel industry, including at BlueScope’s Port Kembla Steelworks.
BlueScope, as the project manager of the NeoSmelt pilot, would build, test and operate the pilot plant. Currently in the pre-feasibility stage, the objective is to have the pilot facility operational in 2028. The pilot plant would produce 30,000 to 40,000 tonnes of molten iron per year.
“This announcement marks a significant milestone in what is truly a unique and transformative project to help decarbonise the steel industry. The progress made during the pre-feasibility stage is a testament to the collaboration of all parties involved.
“BlueScope’s role as Project Manager leverages our deep iron and steelmaking experience at the Port Kembla Steelworks and our unique capability as the operator of the world’s only electric smelting furnace processing Direct Reduced Iron (DRI) in New Zealand.”
Tania Archibald, Chief Executive Australian Steel Products, BlueScope
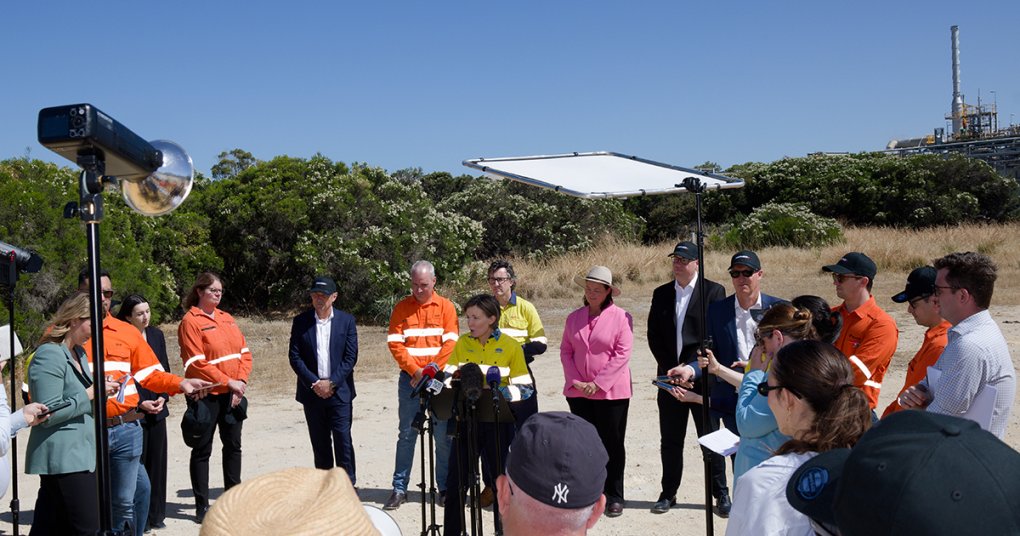
Why is it important to decarbonise iron and steel production?
Iron and steel production
- Steel is the world’s most widely used metal, forming the backbone of infrastructure, transport, and construction. It also plays a key role in the global transition toward decarbonisation.
- Iron and steel manufacturing is responsible for about 8% of global CO₂ emissions.
- Traditional steelmaking processes rely on metallurgical coal and blast furnaces.
Why NeoSmelt?
- For Pilbara iron ore, a promising lower-emissions steelmaking approach would involve direct reduced iron (DRI) with an electric smelting furnace (ESF).
- The NeoSmelt pilot plant aims to test and optimise iron production using the ESF - a type of furnace being developed by leading steel producers and technology companies targeting lower-emissions3 intensity steel.
Further information
- Read BlueScope’s news release - BlueScope, BHP and Rio Tinto select WA for Australia’s largest ironmaking ESF pilot plant
- Watch video - Electric Smelting Furnace (ESF): a Bridge to Low-emissions Ironmaking
- For more information about BlueScope’s decarbonisation pathway in Australia, read our Climate Action Report